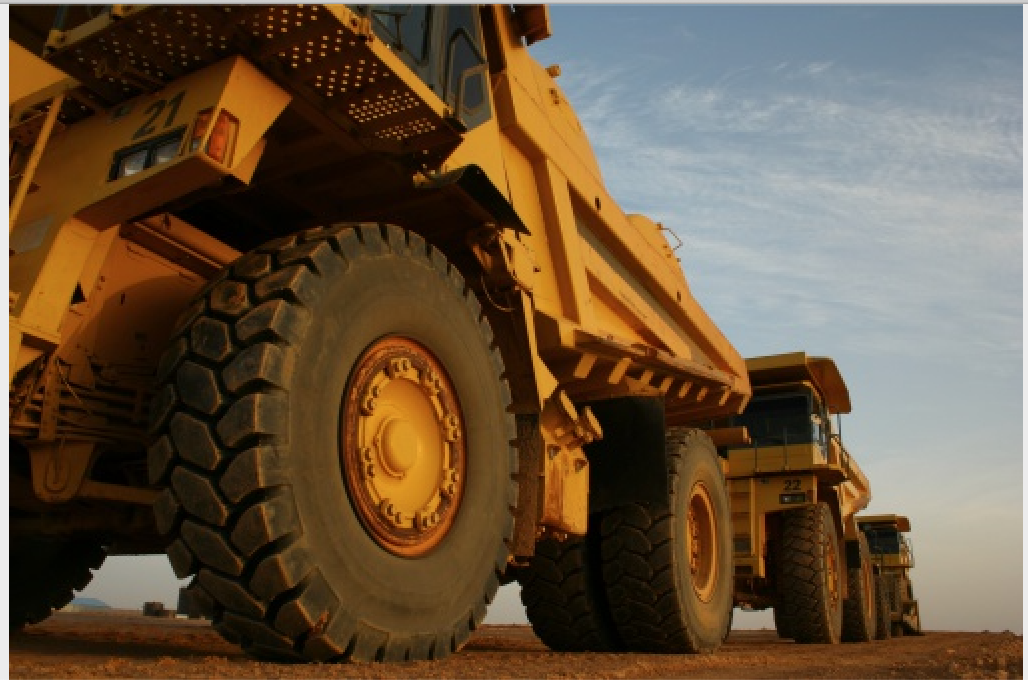
By managing equipment effectively, construction companies can remain competitive and agile, even during periods of economic uncertainty. Here are eight steps to help...
Construction companies manage multiple projects simultaneously with the hope of achieving maximum productivity on a daily basis, even with limited resources. All active construction job sites cannot operate without having an adequate fleet of equipment, which requires seamless scheduling throughout the different phases and through completion. While it is exciting to think about that new piece of yellow iron sporting your famous logo for all to see, it is far more important to perform the cost analysis before you sign the contract to ensure that a potential tax benefit will actually work for your company—and that you’ve got a viable plan to recover the cost outlay in a reasonable period of time. You should also consider what the marketability might look like in the event of a lost project or economic downturn.
As impressive as it may seem to have a fleet of equipment in a contractor’s yard, it should be operating at active job sites for as many days and hours as possible. It is a well-known fact that construction companies face challenges with respect to forecasting equipment needs and managing utilization on a long-term basis due to various circumstances. Challenges are often mitigated if the companies have multi-year and multi-billion-dollar contracts for which contractors can recover not only the cost of equipment, but the cost of maintaining equipment, too. Many contractors work on projects that last less than 24 months, whereas equipment purchased for projects typically has an estimated useful life of at least five to seven years.
Listed below are key steps you should consider for establishing best practices for equipment management, all for the sake of staying competitive and being agile in the event of economic change.
Step 1: Know what inventory equipment you have on hand
How often do contractors take a physical inventory of the equipment on hand? In order to have a better understanding of the finite resources you have, it is recommended that contractors take a physical inventory and make an assessment on the overall condition and operating issues associated with each piece of equipment on an annual basis (at minimum). During this process it is recommended that you review each piece of equipment’s downtime, repair costs, and foreseeable part replacement needs. You should also assess whether any ineffective or underutilized equipment should be replaced by examining operating hours, cost of repairs, and maintenance, as well as past and anticipated future utilization. Evaluate whether any old equipment should be retired and disposed of. Personal property taxes are assessed on each piece of equipment as long as they remain in the hands of the contractor—regardless of whether or not they are in use.
Step 2: Evaluate equipment output capacity in hours
Based on the equipment inventory and study performed in Step 1, the project output capacity of each equipment unit in hours. Maximum output capacity is deemed 2080 hours (40 hours x 52 weeks). However, contractors can encounter weather, temperature, unforeseeable delays in a project after mobilization of equipment, and other factors, all of which prevent equipment from realizing full utilization. Geographic and project-specific conditions may also have a significant impact on the contractors’ equipment utilization. Actual annual utilization may range from 50% to 60%, or 1,040 or 1,248 hours, as all equipment is not equally called for by construction projects. Upon completion of the evaluation, calculate both total equipment output capacity and total equipment output capacity per equipment type in hours. (See step 5 for an example of the equipment rental rate calculations using output capacity in hours.)
Step 3: Reassess equipment needs based on backlog or bidding phase
The equipment division should work closely with the project managers and foremen to schedule out equipment needs on an ongoing basis. A best practice would be the early coordination between the estimating division and equipment division, outlining probable upcoming equipment needs. That way, you ensure availability or alternate options. If a conflict of equipment usage is identified during the pre-bid or bid phase, contractors could then consider an acquisition of additional equipment for a new project and financial resources may be secured at this time. Consider whether a lease option is available for the duration of a potential project and obtain a quote of the rental rate including taxes, insurance, and any other maintenance costs.
Step 4: Calculate the operating costs of maintaining equipment
The equipment division should perform a cost study in conjunction with maintaining the equipment on an annual basis. It is a best practice to perform a maintenance cost study by type of equipment, which provides more precise information and keeps a contractor more competitive in the market. This cost study should be updated at least annually in order to capture the impact of annual cost of living adjustments (maintenance labor costs), fluctuations and volatility of fuel costs, repair parts to be carried on hand, and an increase in storage/rental costs. This is an extremely important process to ensure a recovery of the total maintenance costs and to earn (hopefully) a profit of operating equipment division.
Year 20X1
Excavators | A | B | C |
---|---|---|---|
Utilization (hours) | 1,550 | 1,025 | 750 |
Repair and maintenance | $6,000 | $4,200 | $2,100 |
R & M rate per hours | $3.87 | $4.10 | $2.80 |
Average repair and maintenance rate = $12,300 divided by 3,325 hours $3.70
Year 20X2
Excavators | A | B | C |
---|---|---|---|
Utilization (hours) | 1,700 | 1,400 | 1,200 |
Repair and maintenance | $8,500 | $7,000 | $4,800 |
R & M rate per hours | $5.00 | $5.00 | $4.00 |
Average repair and maintenance rate = $20,300 divided by 4,300 hours $4.72
The above annual cost studies provide an insight as to a trend of rising repair and maintenance costs, as well as an opportunity to evaluate whether the rental rate should be adjusted for cost of living, labor, and benefit rates, or whether the equipment is to be replaced.
Step 5: Calculate the cost of equipment and effective rental rate
Equipment cost consists of its purchase price, sales tax, shipping and installation costs, and financing charges at the time of acquisition of the equipment. For example, an equipment cost of $100,000, sales tax of $8,750, the shipping cost of $2,500, and no financing charges amount to $111,250. If its annual utilization is assessed at 1,250 hours—or approximately 60% utilization per year—and its estimated useful life in accordance with the contractor’s accounting policy is five years, and hourly equipment cost is substantially higher than a 100% utilization rate of $10.70 ($111,250 divided by 10,400 hours). Equipment cost is calculated to approximate $17.80 per hour ($111,250 divided by 6,250 hours). Keep in mind that this amount does not include any other costs associated with the annual holding costs, such as insurance and personal property tax.
The effective rental rate consists of all of the costs for the equipment purchase plus parts, fuel, maintenance costs, outside repair costs, insurance, and other costs of maintaining the equipment for the estimated useful life. Based on the contractor’s historical experience, let’s assume that this type of equipment generally requires maintenance cost approximately 25% of the equipment cost, 30% of the equipment cost as fuel and oil costs, 10% of the equipment as storage costs, and 10% as parts. Total effective rental costs amount to $111,250 + $25,000 + $30,000 + $10,000 + $10,000 = $186,250. Hourly effective rental rate is calculated to be $29.80 ($186,250 divided by 6,250 hours). This is the rate to be recovered from a project if this equipment is dispatched. A reasonable mark-up on the calculated cost should be considered and applied in order to generate a profit from the equipment division.
Equipment Cost | Maintenance | Fuel and Oil | Storage Cost | Parts | |
---|---|---|---|---|---|
($) | $100,000 | $25,000 | $30,000 | $30,000 | $10,000 |
% to Equipment | 100% | 25% | 30% | 10% | 10% |
Output (hours) | 6,250 | 6,250 | 6,250 | 6,250 | 6,250 |
Cost/Hours | $16.00 | $4.00 | $4.80 | $1.60 | $1.6 |
Cost Type | Rate/Hour |
---|---|
Equipment | $16.00 |
Maintenance | $4.00 |
Fuel and oil | $4.80 |
Storage | $1.60 |
Parts | $1.60 |
Use tax | $1.40 |
Shipping | $0.40 |
Total Cost | $29.80 |
Step 6: Compare the effective rental rate against the cost for a rental option
If a quote for a rental option is less than your effective rental rate per hour and the project for which the equipment was purchased lasts less than the estimated useful life of the equipment, the rental option might be the more cost-effective option. If there are no other secured projects to consume the remaining estimated useful life of the equipment that was determined to drive the break-even point, then a straight purchase could be cost-ineffective. However, you should also look at a resale value and apply that as well. If the equipment is readily marketable and easily auctioned at a fair value, a straight purchase and resale of the equipment may provide a more cost-effective approach. It is too expensive to maintain the equipment unless one project for which the equipment was purchased recovered the entire effective rental cost. Again, reassess whether the equipment should be kept for future projects or disposed of—given there is no foreseeable usage for the near future.
Step 7: Mark-up on calculated effective rental rate for a bid
Once the total cost of using equipment to provide services is established as an effective rental rate, you may consider what a competitive and reasonable mark-up percentage should be. Heavy and civil contractors may have to use a required equipment rental rate provided by the Department of Transportation and may not have an opportunity to explore. After calculating the effective rental rate, compare the equipment rental rate provided by the Department of Transportation and analyze whether your effective rental rate is reasonable or discounted. If it is discounted, you are missing an opportunity to generate additional cash inflows. Maintaining your effective rental rate per equipment will help you make a decision on pursuing a project or marking up an additional percentage on other line items or services in a contract to recover the discounted equipment rental rate.
Step 8: Prepare to be agile for economic downturn
Market values of used construction equipment fluctuate significantly due to the law of demand and supply. It is best not to carry extra equipment for which its utilization is uncertain and limited for future opportunities because regulatory changes may require additional refurbishing costs. In addition, unnecessary costs for non-operating equipment would impact financial reporting. As soon as its limitation is identified, consider disposing of the idle equipment for cash or for trade-in credit while the idle equipment is in demand. It will minimize an impact from depreciation expense, insurance, property taxes, and maintenance costs on the contractor’s net income for the financial statement reporting purpose. During an economic downturn, it is extremely critical to stay in compliance with financial ratio covenants imposed by a lender and to proactively manage those costs before others react to the downturn.
How we can help
At CLA, we take the time to understand your specific business so we can help you figure out the best course of action for your business. This certainly applies to equipment management, which is a key skill for being successful in the construction industry. Though it is a time-consuming and ongoing exercise, having a clear understanding of equipment maintenance costs can help contractors when making critical strategic decisions.